Brechbuhler Scales, Inc. Nitro Assists in a System Overhaul with Two DD 1050i’s
Phase 1:
The customer was in an unfortunate predicament, in terms of their business process, when their very old GE Fanuc PLC system crashed on them. They decided to get the person who originally did all of their logic programmings, but unfortunately, this gentleman passed away several months prior, unbeknownst to them. They were also using a Rice Lake 920i indicator, with 6 scales attached to it. The indicator also had a custom program in it that we could not access due to needing a specific file, with a particular extension… which the deceased gentleman also had that we could no longer get.
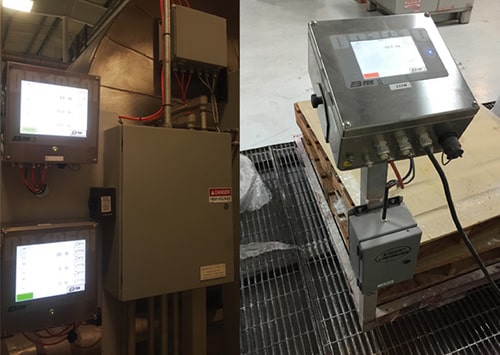
As an answer to their predicament, their new IT person hired a firm out of Atlanta, GA to replace the system with a newer GE PLC system. This system required a different type of communication protocol that was being used before with the 920i and the GE Fanuc, and the B-TEK/Brechbuhler team stepped up and was able to come up with a solution; enter the Diade system! We thought that some of their past issues with losing communications in the old system, software lockups, and incorrect weights might have had something to do with the fact they were pushing a total of (12) 350Ohm tank mount load cells, and (12) 360Ohm floor scale load cells, all with significant distances for homerun cables, and junction boxes for each one, with just the one 902i. This left a lot for the old indicator to handle, so we decided to split the job up between two DD 1050i smart indicators.
The indicators had a custom program written to better incorporate them into their new PLC system. We created a custom ASCII string that would transmit to an RTA module, via TCP/IP, which converted to MODBUS registers over TCP/IP. The program also had to have an adjustable millisecond output to the RTA module, due to the timing of the three different scales’ output being sent into the one string. The RTA module was utilized on previous projects and was found to work very well in industrial environments; similar to what would be experienced at the manufacturing company. These modules communicate directly to the DD 1050i on a specific port, and can be placed anywhere on the network, provided it is in the same SUBNET as the indicator. This made their installation that much easier because it didn’t need to be in close proximity to where the indicators had to be mounted.
After the software was developed to the customer’s specifications, the installation was completed and tested. There were some issues with the timing of the data string to fit the MODBUS registers just right, but with the adjustable timing field in the setup, we overcame this fairly quickly! Upon weighing a batch of product for the first time after installation, it was found that one of the tank mount scales was having issues. We investigated and found out that the three existing hoppers were installed by a company from Texas, and had never been calibrated by Brechbuhler personnel. These three happened to be attached to their new indicators. After finding a problem with one of the hopper’s load cell mounts, repairing the bolt-hole pattern to reduce binding, and recalibrating with more weight, the customer was satisfied that the hopper was weighing great!
Phase 2:
The customer had been using an old MSI CellScale 9000 wireless weighing system, to transmit three of their portable floor scales’ weight to the old Fanuc PLC. We had previously been out several times to troubleshoot, then calibrate/repair as needed, and the process was tedious, to say the least; it required a laptop communicating to the CellScale’s serial port, via Hyperterminal, and each individual “Channel” had to be calibrated this way. The fact that the new PLC system didn’t have a serial port to communicate with these devices left them with zero system-wide weighing on these scales. The customer asked us for a solution to this after the successful installation of the two DD 1050i indicators.
Since the current indicators acted as a “remote display” that read from a CellScale 9020, which received the A/D counts from the CellScale 9000, which transmitted over the proprietary wireless system, we wanted to minimize the failure points in the system by cutting out as much hardware as possible. A solution was found in three DD 1010i indicators that were attached to Antaira APN-210N network bridges. Since it was an industrial application, we decided to place the APN-210N into a custom enclosure that better fits the environment. The existing Diade application was modified for a one-scale-to-one-indicator, but all three ASCII strings were transmitted to a single RTA module. It was discovered that this application would work better since each device’s string was separately going into the RTA module. The system was tested and found to be working well with the customer’s new PLC system and custom weighing software.
The entire project addressed the customer’s many technical needs, from a MODBUS communication solution to the portable weighing systems, we met and exceeded the customer’s expectations. We have already been in talks with extending their usage of Diade indicators to the many individual reactors they’ve been purchasing as well, and look forward to a long and fortuitous business relationship between the customer, Brechbuhler/B-TEK Scales, and the Diade line of programmable indicators.